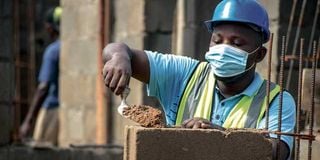
Substandard building materials entering the country unchecked are slowly killing local companies.
Over the past few years, the construction industry in Kenya has witnessed a notable surge in the cost of building materials, largely due to increase in costs of importing raw materials.
According to a recent report by the Architectural Association of Kenya (AAK), the cost of construction surged from between Sh34,650 and Sh77,500 per square metre at the beginning of 2023 to between Sh41,600 and Sh100,800 by December 2023. The surge was attributed mainly to the increase in costs of materials, with goods such as steel used in reinforcement bars, doors, windows, beams, columns and roofing sheets, rising from Sh140.60 per kg in December 2022 to Sh160.26 per kg in December 2023.
Meanwhile, the cost of cement rose from Sh650 per 50 kg bag in December 2022 to Sh750 in December 2023, marking an approximate price increase of 15.38 percent. The situation persists, with Hope Tamara, the General Manager of Imarisha Mabati roofing company, noting that virtually all aspects of building have become more expensive. Roofing, for instance, which would constitute three to eight percent of the total project cost, now represents 10 to 20 percent of the total cost, according to estimates, depending on the type of roofing.
“The high costs associated with construction are discouraging people from buying into projects. Unable to sell properties as quickly as they would want, developers are shying away from adding more projects to their portfolios,” notes Tamara. This of course is affecting the local producers of construction materials, many of whom are having to contend with lower sales and profit margins, with some having to downsize their staff and operations to remain afloat.

President William Ruto lays the foundation stone for the construction of affordable housing units in Buuri, Meru County, on Thursday, January 25.
“Construction projects are facing budgetary constraints and potential delays, posing challenges to the sector’s growth and development,” says Tamara. The rising insecurity at key trading routes such as the Red Sea has only exacerbated the situation, as vessel owners are having to go for alternative shipping routes that are safer, but longer, pushing freight charges up by up to 70 percent on average. From about 14 days through the Suez Canal, vessels are now taking up to 48 days to ship goods through alternative routes such as the Cape of Good Hope in Southern Africa, which is nearly three times longer.
“The vessel owner will pass on the additional shipping costs to us, the importers, and we in turn are forced to pass the costs incurred in shipping and production down to the consumer in order to break even,” says Tamara.
Arguably, this is affecting the profitability of companies engaged in the production of construction materials, as consumers are instead opting for cheaper imports from foreign companies.
“Many foreign companies are coming in with cheaper products of lower quality. Clients will always be excited when they see a lower price on a product, but how much more will it cost them in the long run?” poses Tamara.
Stakeholders such as herself are calling on the government to control the promotion of substandard building materials imported from other countries by establishing and enforcing strict quality standards.
“This will help to safeguard lives and livelihoods. We have had too many cases of buildings collapsing as a result of the use of substandard building materials.”
Creating an enabling environment for existing businesses to thrive and compete on a level-playing field with their regional and global counterparts, will not only enable them to succeed locally, but also in regional markets. The stakeholders also want the government to help subsidise operating costs for local manufacturers of construction materials by providing them with incentives that will drive their competitiveness and productivity.
Boosting the capacity of local firms to sustainably produce goods and services for which there is a market, at a price and quality that the market is willing to pay for, will enable them to participate in the various infrastructural projects which both levels of government are undertaking, such as the construction of markets.
Competitiveness
Reducing the number of regulations, strengthening local supply chains to reduce reliance on imports and bringing down the cost and time spent on compliance, could help to spur the competitiveness of local manufacturers of construction materials. Continued consultation with all stakeholders in the value chain before implementation of policies is also crucial to ensure that more holistic policies are put into place. With this in mind, regulatory agencies should work closely with industry stakeholders and create avenues for dialogue so as to achieve consensus on what the industry needs, and by extension drive up the standards of quality.

President William Ruto (centre) accompanied by Deputy President Rigathi Gachagua (left), Uasin Gishu Senator Jackson Mandago (second left) and other leaders during the laying of the foundation stone for the construction of Kidiwa Affordable Housing in Eldoret town, Uasin Gishu County on January 9 2024.
Employing more than 200, 000 people, companies engaged in the production of construction materials can be considered major drivers of economic growth. These firms, however, face a myriad of challenges that prevent them from operating at full potential. Some of the challenges that they face include supply chain disruptions, lack of adequate financing, trade issues, quality and environmental concerns, lengthy procurement procedures, poor market intelligence and ineffective regulation.
“We need to be deliberate about creating an environment that genuinely encourages investment in this sector. This can only be made possible through a commitment to actualising policies that make it possible for local manufacturers of construction materials to grow and to expand operations,” states Tamara.
Kenya’s capacity to capture the opportunities present in the industry could also be boosted by better institutional collaboration, tackling constraints related to the supply of raw materials to increase production and quality, as well as improving productivity and innovation through better skills and technologies. Stakeholders are calling on the government to develop policies with a long-term economic view as opposed to short-term goals aimed at raising revenue without considering the impact of such policies on citizens.
An unpredictable tax regime, at times arising from the need to raise revenue to meet expenditure, has hindered the business community from making long-term investment plans. It is, therefore, a challenge for manufacturers to maintain competitive pricing on their finished goods, and it will not be easy on the consumer unless the government comes in to waive off duty on some of these raw materials.
DN Property engaged Mohsin Adamjee, a tax expert, who is of the view that to a large extent, the government deserves credit for some good policies it has created to enhance the competitiveness of local firms engaged in production of construction materials.

Engineers at a construction site.
For instance, under the Finance Act, 2023, the government introduced an export and investment promotion levy, which is now chargeable at the rate of 10 percent and 17.5 percent of the customs value of certain specified imported products, which can be manufactured locally. The move was aimed to boost the manufacturing sectors’ contribution to GDP from the current 9 percent to 15 percent by 2027. Some of the goods that are targeted by the export and investment promotion levy are steel products used in construction. The government also recently introduced a Value Added Tax exemption program that seeks to encourage more developers to participate in the affordable housing initiative. Developers who sign up to the program are to access building materials at a subsidised cost, for them to make a profit while building the affordable houses.
The government has also directed that 70 percent of the construction materials used in the development of these affordable housing units are to be sourced locally.
“Such policies can drive job creation, spur industrialisation and growth of local firms as well as boost the sector’s contribution to GDP,” says Adamjee.
The financial consultant however notes that what has been lacking is the follow up process of implementing such policies, which aim to enhance the competitiveness of local firms.
Import duty
In several situations for instance, state agencies mandated with ensuring that import duty on goods that can be produced locally are paid, have turned a blind eye, leaving room for corruption to take place. Subsequently, cheap imports flood the market at a higher advantage than local goods, distorting prices and eventually causing local companies to shut down. This is dampening investor confidence, with some entrepreneurs switching their attention to alternative markets that offer a higher return on investment. Estimates indicate that it is 12 percent more expensive to do business in Kenya than it is in other East African country.
“When our local companies cannot sell their products, they shut down, cease to offer employment, and our unemployment rate continues to sky-rocket,” states Adamjee.
To spur the growth of local industry, Naftali Oswere, the proprietor of Bantu Homes, notes that it is important to address the issue of lengthy procurement procedures, which may seem minor, but is actually killing businesses. In some instances, buyers, including government contractors, private developers, or even retailers such as hardware operators, fail to pay local suppliers of construction materials promptly for goods delivered. This deprives local firms engaged in the production of construction materials of much needed funds to sustain their operations.
“While retailers pay in advance before importing goods from foreign manufacturers, they pay very late when obtaining the same goods from local suppliers, thus slowing the growth of these enterprises,” notes Oswere.
Such practices have minimised the construction sector’s contribution to the country’s GDP to only about five percent, which is way below the global average of about nine percent.
“When developers and contractors import from China or India, they pay cash in advance for the goods delivered, but when it comes to local manufacturers, they delay payment for several months,” says Oswere.